목차
※ 텍스트를 클릭하여 원하는 위치로 이동하세요.
3D 프린팅으로 고품질의 제품을 제작해 볼까요?
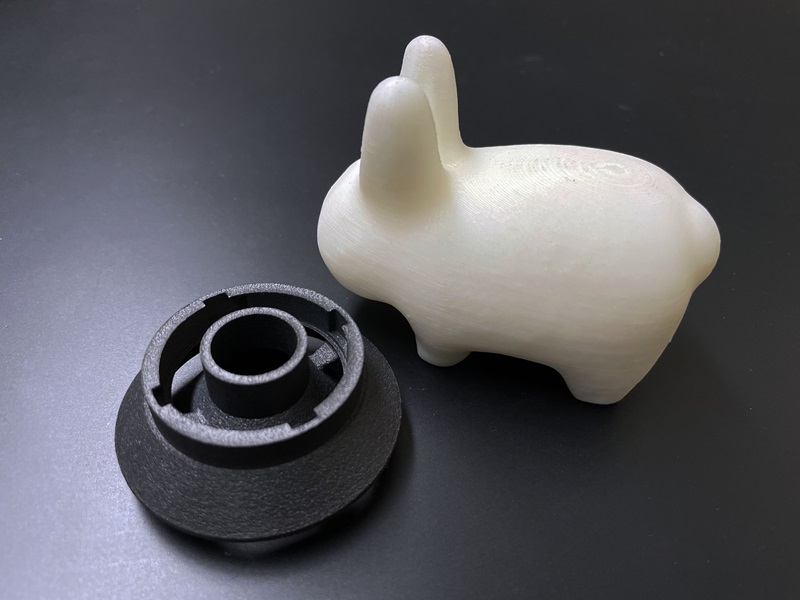
일반적으로 가정이나 학교에서 사용되는 3D 프린터는 FDM 방식으로, 필라멘트를 녹여 적층 후 제작하기에 일정한 수준의 표면 퀄리티를 넘기지 못합니다. 이런 방식의 3D 프린팅을 알고 계시는 분이라면 적층 무늬를 염려하실 수 있습니다. 또 제품 목적이 전시에 있다면, 프린팅 출력물의 퀄리티가 충분히 만족스러울지 의문스러우실 수 있습니다.
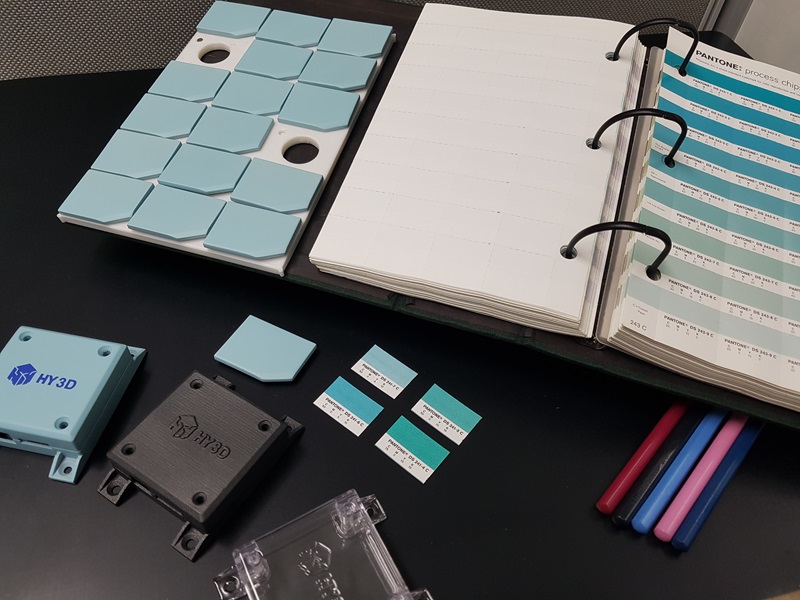
이처럼 퀄리티에 관한 우려 사항이 있을 경우 1. 표면 조도가 우수한 출력 방식을 선택하거나, 2. 후가공을 진행하면 원하는 퀄리티로 제작할 수 있습니다. 특히 각 공법에 따른 처리 이후 제품에 알맞은 후가공 방식을 선택하여 진행하면, 적층 무늬가 남는 방식의 출력물도 고급스럽게 탈바꿈할 수 있습니다.
후가공 방식을 합리적으로 결정하기 위해서는 3D 프린팅 출력물을 처리할 수 있는 후가공 과정의 종류에 대해 알아야 합니다. 이 글에서는 의뢰 기업의 의사 결정을 돕기 위해, 출력물을 기준으로 표면 정리, 도색, 도금과 로고 작업 등 대표적인 후가공 방식을 소개하려고 합니다.
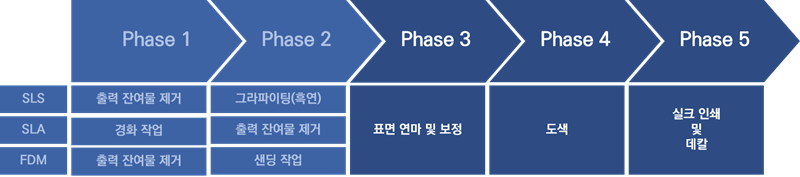
3D 프린팅 이후 진행하는 후가공 과정입니다.
기초적인 후가공과 공법별 후가공 특징은 전편에서 보실 수 있습니다. 전편 바로가기
다음부터는 출력물 퀄리티 향상을 위한 과정으로, 모든 출력물에 필수적으로 진행할 필요는 없습니다. 특히 퀄리티보다 속도나 가성비가 중요한 시제품은 기초적인 후가공 과정만 진행해도 충분합니다. Phase 3부터는 보통 표면 퀄리티가 중요한 전시용 목업에 자주 적용되는 과정입니다.
오늘 다룰 후가공 과정은 모든 출력 방식에 공통으로 적용되는 내용입니다. 크게 다음과 같은 경우에 진행하는 후가공에 대해 다루고 있습니다.
- ● 출력물의 표면 퀄리티를 높이고 싶은 경우
- ● 도색, 도장, 도금이 필요한 경우
- ● 제품에 브랜드 로고를 드러내야 하는 경우
실제 후가공 과정이 궁금하시다면 아래 바로 가기를 눌러 확인해 보실 수 있습니다.
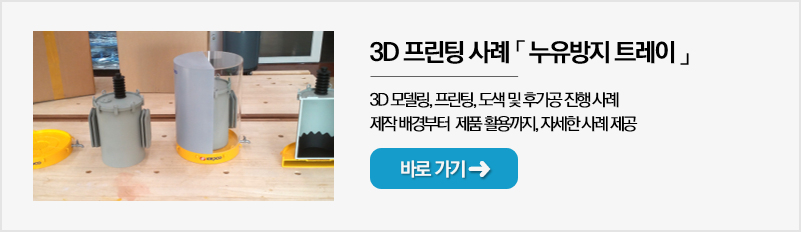
표면 연마 및 보정
3D 프린팅 공법으로 제품을 제작하고 공법별 기본적인 처리를 마쳤습니다. 그러나 여전히 서포터의 흔적이 남아있거나, 서포트가 완전히 떨어지지 않은 부분이 있거나, 표면 조도가 좋지 않을 수 있습니다. 표면 연마 및 보정 과정은 표면을 깔끔하게 연마하는 과정입니다. 샌딩, 퍼티, 서페이서 작업을 적절히 병행하여 제품의 요철을 제거하고, 도색이나 도장, 도금에 알맞은 표면 상태로 만듭니다. 가장 기본적인 후가공 단계이며, 특히 샌딩 작업은 퍼티 작업 이후에 진행하는 등 여러 단계에 걸쳐 실행되곤 합니다.
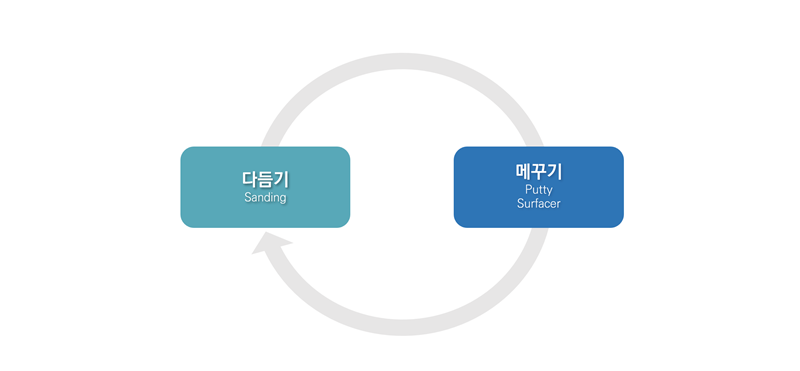
1. 샌딩 작업
제품 표면에 튀어나온 부분이 있거나, 층이 진다면 거슬리는 부분을 제거하고 표면을 매끄럽게 만들어야 합니다. 모래알 같은 연마재를 이용하기에, 이 작업을 샌딩 작업이라고 칭합니다. 제품 용도에 따라, 특별한 퀄리티가 필요하지 않다면 샌딩만 진행할 수도 있습니다.
1) 사포 연마
수작업을 진행할 때는 주로 사포나 줄을 이용하여 요철을 제거합니다. 사포는 연마재 입자가 붙어 있는 천으로, 작은 알갱이가 붙어 있을수록 고운 표면을 연마하기 좋습니다. 실제 제품을 연마할 때는 목적에 따라 다양한 방*의 사포를 골라 사용합니다. 방수가 낮으면 표면을 빠르게 갈아낼 수 있고 높으면 세밀한 연마가 가능하므로, 낮은 방부터 높은 방으로 방수를 높여 가며 사용합니다.
*방: 연마 입자의 크기와 그 밀도를 의미합니다. 방수가 높아질수록 입자가 곱고, 면적당 입자의 수가 많아집니다.
3D 프린팅에서 사포를 사용하는 목적은 다음과 같습니다.
- ① 서포터 제거 후 남은 흔적을 갈아냅니다.
- ② FDM처럼 적층 면이 잘 보이는 공법이라면, 이를 말끔하게 정리합니다.
- ③ 도색을 위해, 표면이 너무 매끄러운 제품을 적당히 갈아낼 때 사용할 수도 있습니다.
- ④ 퍼티 작업 이후, 표면을 한 번 더 연마해 주는 목적으로 사용하기도 합니다.
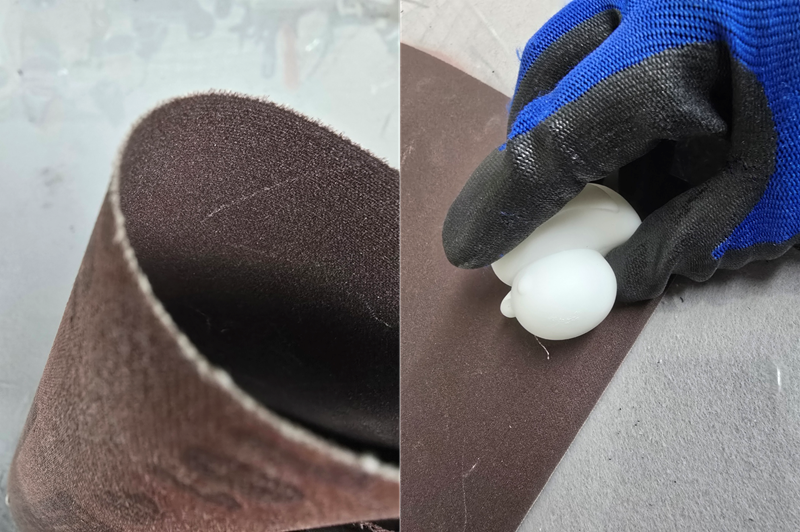
사포를 사용할 때, 습식으로 사용할 수 있는 천 사포에 물을 먹이거나 샌딩 도구에 사포를 감싸 사용하면 더 편한 작업이 가능합니다.
사포를 물에 적시는 이유?
- 사포로 샌딩 작업을 진행하면 미세한 분진이 발생합니다. 이때 습식으로 사용할 수 있는 천 사포에 물을 먹여 샌딩을 진행하면 먼지가 적게 나도록 할 수 있습니다. 이 외에도 발열을 막아주고 더 고운 마감이 가능하도록 도와주지만, 초기 작업처럼 많은 부분을 갈아내야 하는 경우에는 건식 사포가 더 유리할 수도 있습니다.
사포를 사용할 때는 힘을 과하게 주지 않도록 주의해야 합니다. 압력이 가해질수록 마찰면이 과열되기 쉬워지고, 내열성이 약한 소재나 얇은 제품은 변형될 수도 있기 때문입니다.
그에 더하여 과하게 연마하면 복구가 어려워질 수 있으므로 언제나 주의를 기울여야 합니다. 제품 표면의 감촉이 원하는 정도가 되었는지, 표면에 요철은 없는지 확인하면서 작업합니다.
2) 샌드블라스트 작업
더 섬세한 샌딩이 필요할 시에는 샌드블라스트를 이용합니다. 샌드블라스트는 사포와 달리 연마재 입자를 분사하여 표면을 깎아내는 방식입니다. 목적에 따라 사포를 물에 적셔 사용하는 것처럼, 샌드블라스트에도 건식과 습식 장비가 존재합니다.
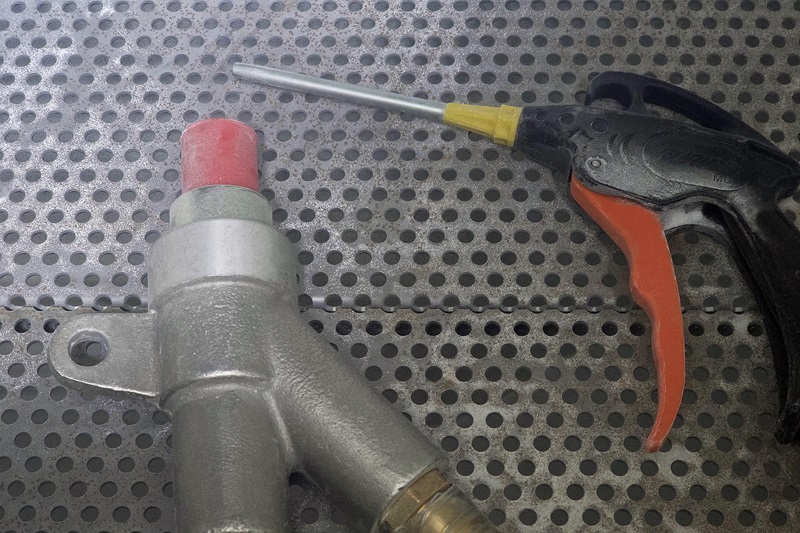
3D 프린팅이 끝난 후, 사포를 이용해 단계별로 갈아내면 표면이 충분히 매끄러워진 것처럼 보입니다. 그러나 사포는 기본적으로 제품 표면을 마모시켜 가공하는 작업이기에 모래 알갱이의 모양에 따라 미세한 요철이 발생한다는 사실을 유의해야 합니다. 작은 출력물이나 사포가 들어가기 힘든 부위에 사용하다 보면 힘 조절이 어려워지고, 표면에 스크래치가 날 수 있습니다.
샌드블라스트는 이런 사포의 단점을 보완하여, 굴곡이나 홈 등 세밀한 표면 처리에 사용됩니다.
- ① 제품 변형을 최소화합니다.
- ② 거칠기 조절을 균일하게 할 수 있도록 도와줍니다.
- ③ 좁은 틈을 세밀하게 작업하는 데 적합합니다.
3D 프린팅 공법 중 SLA(광경화성 수지 조형 방식), SLS(선택적 레이저 소결 방식)로 제작하면 기본적으로 표면 조도가 좋기 때문에 주로 샌드블라스트를 이용해 후가공을 진행합니다.
3) 기타 연마 작업
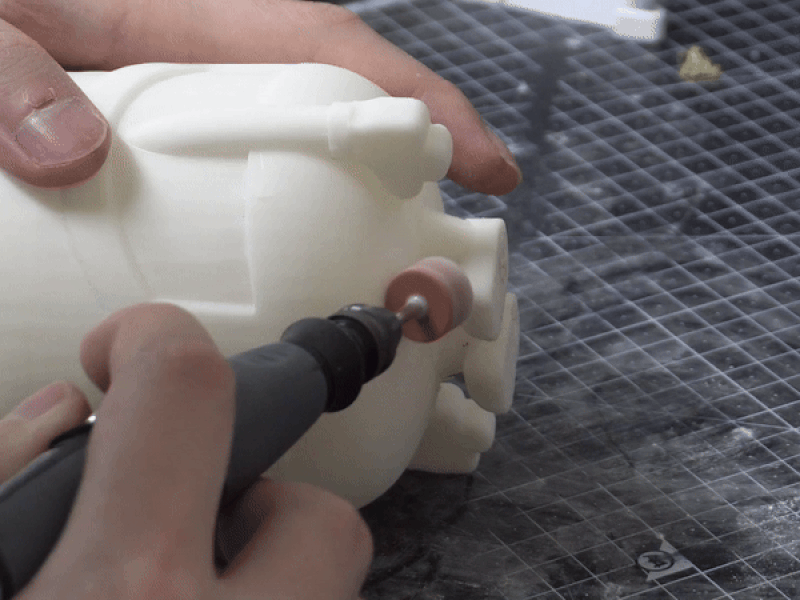
이외에도 다양한 가공 방식이 있습니다. 상황에 맞는 가공 방식으로 3D 프린팅 작업물의 서포터를 제거하고, 표면 퀄리티를 높일 수 있습니다.
- ● 출력 직후에는 훈증기, 연마기와 같은 특수 후가공기기를 사용할 수도 있습니다. ABS-Like의 표면을 매끄럽게 처리하거나, PA12의 오돌토돌한 표면을 다듬고 완성도 높은 외관을 보여주기 위해 그라파이팅 처리를 하는 등 일반적인 사포질과는 다른 작업을 진행합니다.
- ● 모서리나 구멍에 남은 버(burr, 거친 부분)를 제거할 때는 디버링툴을 이용합니다. FDM 프린터는 재료의 경도에 따라 서포터를 말끔하게 제거하지 못하는 경우가 있습니다. 이때 서포터를 떼어내고 남은 부분을 디버링툴로 말끔히 잘라낼 수 있습니다.
- ● 샌딩기는 샌드블라스트와 비슷하게 힘을 균일하게 주기 위하여 사용합니다. 사포를 잘라 끼우는 형태의 핸드 샌딩기를 이용하기도 합니다.
- ● 평줄은 금속에 골이 패여 사포처럼 다듬는 용도로 사용할 수 있는 도구입니다. 주변에서 쉽게 볼 수 있는 손톱 줄도 줄의 일종입니다. 줄칼이라고도 부르며, 사포와는 달리 금속으로 만들어져 있는 경우가 대부분입니다. 깎아내는 양이 많아 모양을 잡는 데 사용하거나, 제거되지 못한 서포터를 갈아내는 데 사용하기도 합니다.
공법과 상황에 따라 가장 적합한 후가공 방법은 달라질 수 있습니다.
2. 퍼티 작업
서포터를 떼어내고, 표면을 갈아내는 기본적인 샌딩이 끝났습니다. 서포터를 떼어내다 말고 흠집을 내거나, 샌딩 작업에서 스크래치가 냈다면 퍼티를 이용할 수 있습니다.
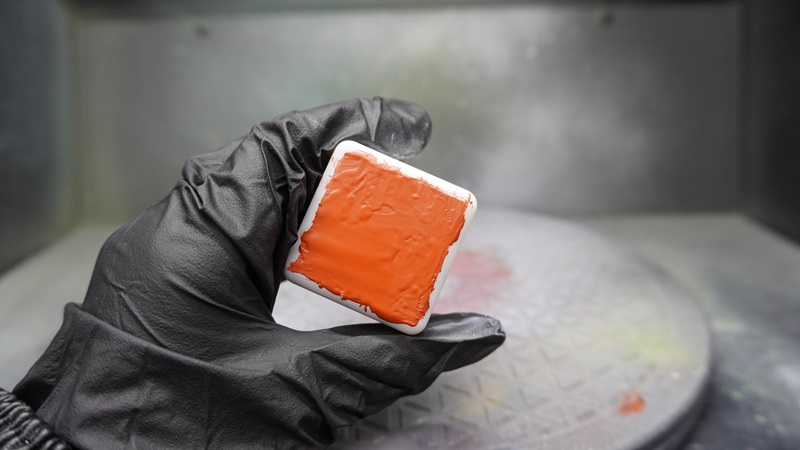
퍼티는 빠데라고도 부르며, 인테리어를 하거나 차량 흠집을 메울 때에 자주 사용하는 접합제의 일종입니다. 타 접합제와는 달리 표면을 균일하게 만드는 데 사용됩니다. 제품 전체를 감싸 바르기도 하고, 접합부나 흠이 있는 부분만을 메우기도 합니다.
FDM으로 프린팅한 제품처럼 표면 요철이 두드러지거나, 적층 흔적이 남는 방식은 퍼티를 이용해 프린트물 특유의 흔적을 가릴 수도 있습니다.
※소재, 후가공 과정에 따른 비용과 제작 기간은 제품 특성에 따라 다를 수 있습니다. 표면 조도가 우수한 SLA 방식이 좋을지, 후처리가 필요한 FDM 방식이 유리할지는 제품 문의를 통해 확인해 드리고 있습니다.
퍼티는 점토와 같이 매트한 질감을 가지고 있습니다. 보통 퍼티 작업 시에는 주제와 경화제, 물을 적당한 비율로 섞어 도포합니다. 이후 퍼티가 굳어버리기 전에 얇게 펴 바르고, 마른 다음에는 도포 자국을 없애기 위한 샌딩을 진행합니다.
퍼티 작업 직후의 표면은 바른 모양대로 굳어 울퉁불퉁하며, 제품 형상이 작고 복잡해질수록 고르게 펴 바르기 어렵습니다. 또한 샌딩 이후에는 퍼티의 두께에 따라 기존 제품 면이 얼룩덜룩하게 드러날 수 있어 도색을 진행해야 합니다. 다른 작업과 병행할 때 좋은 결과를 내는 후가공 방식 중 하나입니다.
3. 서페이서 도포
샌딩 작업, 퍼티 작업 등 선행 작업이 끝났다면 표면이 원하는 수준까지 연마되었는지 확인해야 합니다. 또 도색을 염두에 두고 있다면 도료가 잘 부착될 만한 환경을 만들어 주어야 합니다. 서페이서를 도포하면 표면 연마 단계를 확인하거나, 마무리할 수 있습니다. 샌딩이 어려운 형상의 제품에 한하여, 퀄리티에 대한 합의가 되었을 시에는 서페이서 도포만 진행하고 에어브러시 도색으로 넘어가기도 합니다.

서페이서는 무채색의 특수 도료로 도화지를 만드는 역할을 합니다.
- ① 매끄러운 표면이나, 색상이 짙은 표면을 말끔하게 덮어 칠하고자 하는 색상이 잘 올라갈 수 있도록 합니다.
- ② 서페이서를 도포하면 흠집이 잘 보이게 되어 표면 상태를 확인하기 쉽습니다.
- ③ 제품 표면의 미세한 스크래치는 이 과정에서 메워지기도 합니다.
서페이서를 사용하기 전에는 송진포나 정전기 방지 브러시, 먼지 제거기 등으로 먼지를 제거해야 합니다. 샌딩 후에 남아있을지 모를 먼지를 제거하고 작업해야 도포를 말끔하게 완료할 수 있습니다.
이렇게 표면 연마 및 보정 과정이 끝났습니다.
작업 과정에 익숙하면서도 각 3D프린팅 소재에 맞는 가공 방식과 연마 방식을 알고 있어야만 소재가 상하는 일 없이 말끔한 표면을 결과물로 얻어낼 수 있습니다. 예를 들어, ABS-Like는 PLA와 비교하여 샌딩 시 압력을 더 조심스럽게 조절해야 합니다. 같은 압력에도 더 깎여 나갈 수 있는 재료이기 때문이며, 이런 물리적/화학적 특성을 모른다면 제작 과정에서 낭패를 겪을 수 있습니다. 전체적인 과정을 고려하기 어렵다면 3D 프린팅 경험과 후가공 경험이 풍부한 전문가에게 맡겨야 하겠습니다.
도색
표면 정리 및 보정이 끝났다면 이제 제품에 색을 입힐 수 있습니다. 전시용 목업이나 의료 모형이 필요하신 경우에 퀄리티를 높이고, 부품별 색상을 눈에 띄게 하기 위하여 많이 진행하곤 합니다. 투명한 제품을 구현하고자 할 때에도 투명 도료를 바르기 위해 해당 과정을 거칩니다.
1. 에어브러시 도색
에어브러시는 도료를 스프레이 방식으로 도포하는 도구입니다. 이렇게 에어브러시로 도색을 진행하면 붓보다 균일하게, 여러 색상을 표현할 수 있다는 장점을 가집니다.
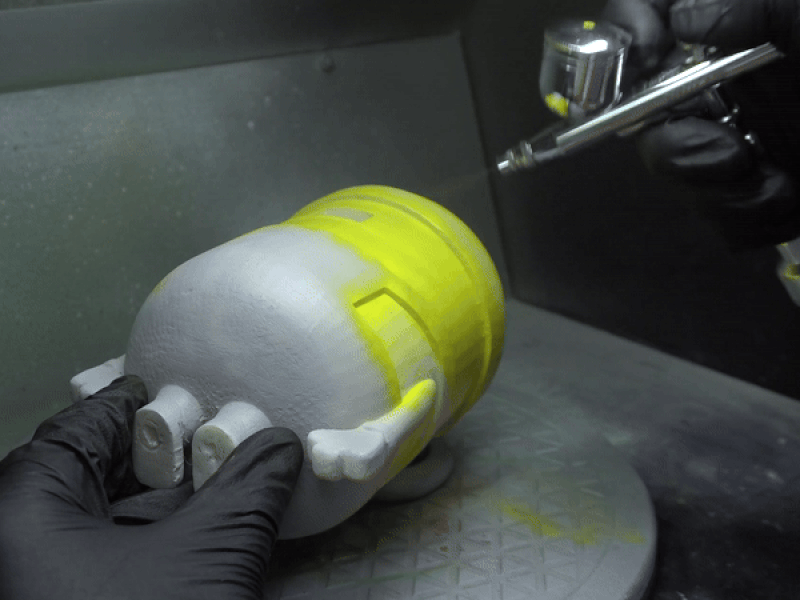
3D 프린팅 분야에서는 제품을 녹이지 않는 성질의 에나멜 도료, 락카 계열 도료 등 다양한 유성, 수성 도료를 에어브러시에 넣어 사용합니다. 여기서는 유성 도료 중에서도 락카 도료를 기준으로 설명드리겠습니다.
에어브러시 도색에서 락카가 가진 특성은 다음과 같습니다.
- ① 유광, 반광, 무광 도료로 다양한 광택을 구현할 수 있다는 장점을 가지고 있습니다.
- ② 발색이 다양하고 우수해 CMYK 코드 중 원하는 색상을 표현하는 데 적합합니다.
- ③ 도색 후 피막이 강한 편이기에 잘 지워지지 않습니다.
- ④ 건조까지 걸리는 시간이 타 유성 도료에 비해 짧은 편입니다.
- ⑤ 락카 도료의 일부는 금속 느낌을 구현하는 데 유용하게 사용됩니다.
그중에서도 메탈릭 도료는 작은 금속 입자가 섞여 있는 도료로, 실제 금속과 유사한 광택을 냅니다. 도금 작업보다는 가성비가 좋은 축에 속하고, 열처리가 필요하여 소재가 한정되는 도금 작업보다 다양한 제품에 적용할 수 있습니다. 샌딩을 최대한 매끄럽게 진행한 뒤 까만 유광 도료를 바르고, 메탈릭 도료를 뿌려 마감하면 빛 반사가 되는 매끄러운 금속 면을 재현할 수 있어 전시용 목업에서 에어브러시 도색을 선택하는 의뢰 기업도 많습니다.
2. 컬러 프린팅
컬러 프린팅은 색상을 지정하여 출력하는 방식으로, 협의된 색상을 프린터기에 입력하여 출력할 수 있습니다. 색상은 보통 CMYK를 기준으로 하지만, 프린터기에 따라 팬톤 컬러 차트 등 다른 기준을 이용하기도 합니다.
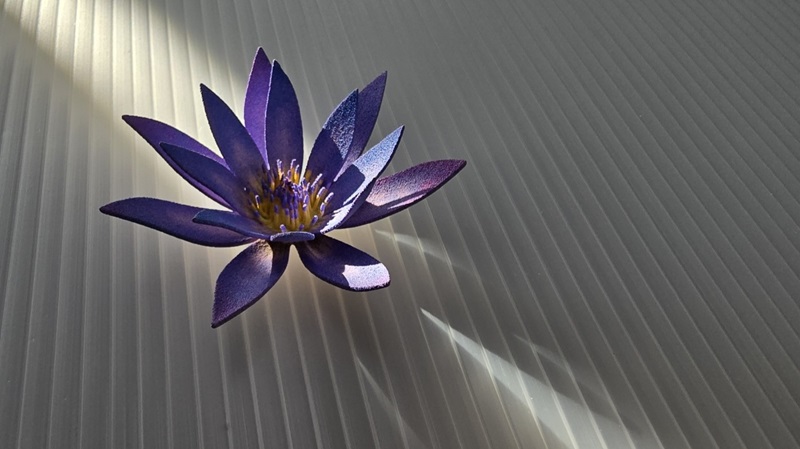
이 도색 방식은 프린터기 자체적으로 색상을 내는 방법이니만큼, 다양한 장점을 가지고 있습니다.
- ① 도색이 어려운 부위에도 색상을 낼 수 있습니다.
- ② 활용할 수 있는 소재가 다양합니다. 합성 고무 소재에도 전체적인 색상을 적용할 수 있습니다.
- ③ 투명하게 출력할 수 있는 소재와 함께 사용할 시, 제품 내부의 색상을 확인할 수도 있습니다.
사진의 보라색 꽃은 복잡한 출력이 가능한 SLS 공법으로 제작되었습니다. 작업을 여러 번 진행할 필요 없이, 꽃술과 같이 얇고 세밀한 부분에까지 도색이 잘 완료되었음을 확인하실 수 있습니다. 꽃잎 바깥쪽과 안쪽의 그라데이션도 수채화 칠을 한 것처럼 자연스럽게 표현되어 있습니다.
합성 고무 소재는 실리콘 등 말랑하고 탄성이 있는 소재를 의미합니다, 제작 과정에서부터 색을 지정하면 투명, 백색, 흑색의 기본적인 색상 외에도 팬톤 컬러 차트 내에서 다양한 색상을 뽑아 활용할 수 있습니다. 합성 고무 소재의 특성이나 도색에 관해서는 아래 게시물을 참조하실 수 있습니다.
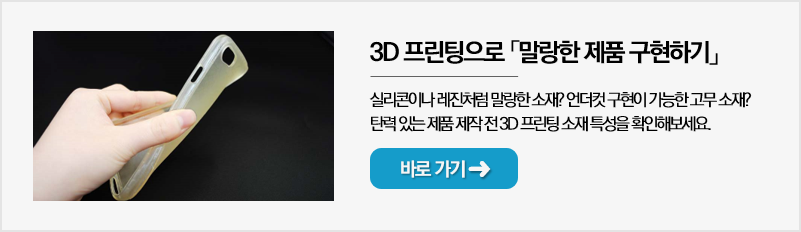
이 외에도 복잡한 형상 제작 시 따로 결합하는 과정이 불필요한 3D 프린팅 공정의 특징상, 투명하거나 다양한 높은 퀄리티의 제품 제작이 가능합니다. 예를 들어 의료용 모형은 투명도 있는 소재와 함께 사용하여 내부 구조 이해를 돕는 등의 활용이 가능합니다.
3. 크롬 도금
크롬 도금은 표면에 얇은 크롬층을 형성시키는 도금 방식입니다.
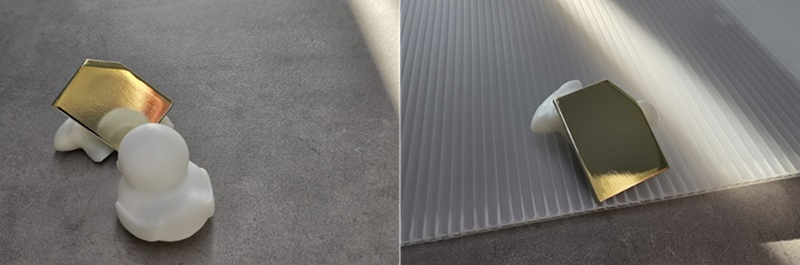
크롬 도금의 특성은 다음과 같습니다.
- ① 내구성이 우수하고 경도가 높습니다.
- ② 표면에 피막을 형성하여 제품을 보호하는 성질이 있습니다.
- ③ 제품의 금속성 표면을 나타내는 방식 중 우수한 퀄리티를 보여줍니다.
크롬 도금 시에는 열처리를 이용합니다. 어느 정도 내열성이 있는 제품이 아니라면 외부가 녹아내리므로 고온을 견딜 수 있는 소재의 제품에만 적용할 수 있습니다. 메탈릭 락카는 제품마다 성능이 다르고, 다루기가 까다로워 작업 과정에서 경면 손실이 일어나는 경우가 종종 있습니다. 표면이 하얗게 일어나는 백화 현상이 나타날 가능성도 있습니다. 그에 반해 크롬 도금이 완료된 면을 보면, 주변 물체가 거울처럼 깔끔하게 비치는 모습을 확인할 수 있습니다. 도금 작업이 진행된 제품은 고급스러운 느낌을 주며, 비교적 스크래치나 환경 변화에 강합니다. 지문이나 오염물이 붙어도 처리가 쉽고, 자외선에 노출되어도 락카에 비해 변화가 거의 없습니다.
이러한 지속성 때문에 금속성 제품의 축소 모형 등을 제작할 때는 높은 비용을 감수하고 크롬 도금을 선택하기도 합니다.
4. 기타 도색 방식
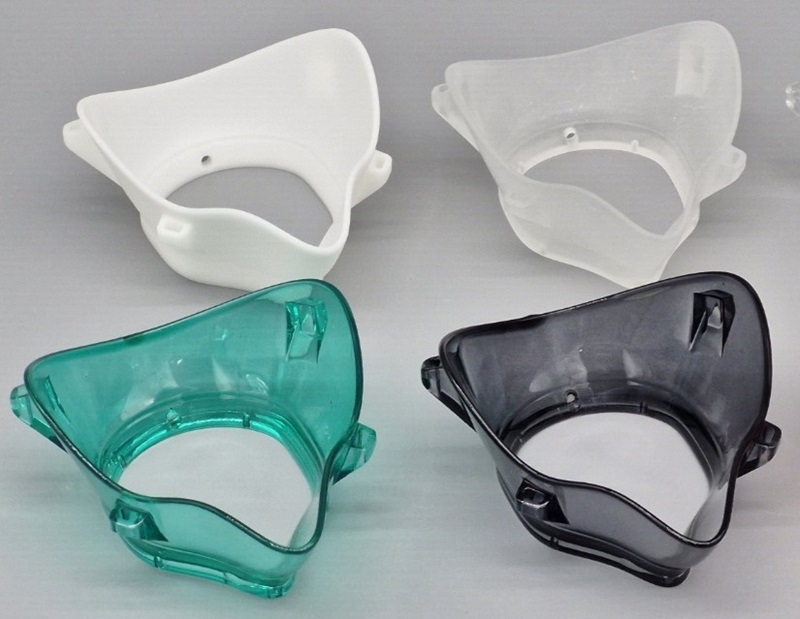
특수한 도색이 필요하다면 다음과 같은 부분도 고려할 수 있습니다.
- ● 투명 소재의 경우, 투명도를 유지하며 색만 바꾸는 염색을 이용할 수 있습니다.
- ● 붓을 이용해 세밀한 부분을 채색하는 방법이 있습니다. 고른 도료 분포를 위해 전체 도색에는 거의 사용하지 않는 방식입니다.
전체 도색 과정을 알고 상담할 수 있는 전문가에게 문의하는 것이 필수적입니다.
실크 인쇄 및 데칼 작업
1. 실크 인쇄
실크 인쇄는 주로 여러 제품에 로고를 부착해야 할 때 사용되는 방식입니다.
실크 인쇄 과정에서는 로고에 맞는 실크 스크린 망을 제작하여 그 구멍을 통해 이미지를 전사합니다. 스퀴지라 불리는 도구로 잉크를 얇게 펴 바르면 막히지 않은 부분에 색이 올라가는 식으로 로고를 인쇄합니다. 잉크 층이 두껍고 선명하여, 다양한 소재의 기판에 색을 올릴 수 있다는 장점이 있습니다. 또 모양에 따라 여러 색상의 잉크를 사용할 수 있어 로고의 색상도 다채롭게 표현 가능합니다.
수작업 시 작업자의 숙련도에 따라 로고 외곽이 번지는 등 실패할 확률이 있으며, 한 번 찍힌 로고는 수정이 어렵습니다. 로고가 복잡한 모양과 색상, 세밀한 간격을 가지고 있을 때에도 다시 숙고해보는 게 좋습니다.
2. 데칼 작업
붓으로 구현하기 힘든 미세한 로고와 숫자, 문자는 데칼 작업을 통해 구현하게 됩니다. 데칼은 일반적으로 생각하는 스티커와 달리 그림과 칼선 사이에 간격을 두지 않습니다. 타투 스티커나 판박이 스티커와 비슷한 방식으로, 로고를 붙인 티가 거의 나지 않습니다. 건식 데칼과 습식 데칼이 있어 용도별로 사용합니다.
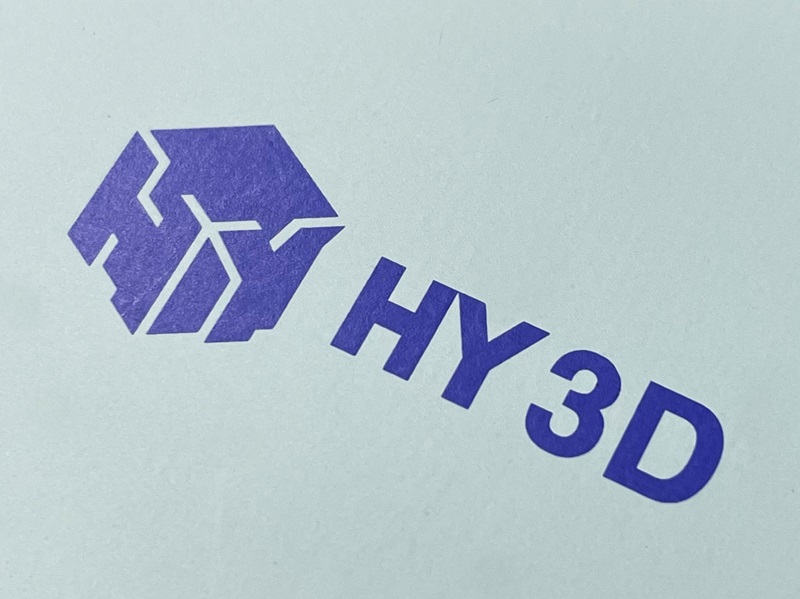
복잡한 로고를 간편하게 부착할 수 있고, 비용 또한 합리적이라 많은 경우에 애용되는 로고 작업 방식입니. 다만 따로 코팅 처리를 진행하지 않고 데칼이 부착된 부분에 충격을 가할 시에는 로고가 벗겨질 수 있습니다. 또 도료 코팅을 락카로 진행하면 로고 표면이 갈라질 수 있으므로 주의가 필요합니다.
3. 마스킹 작업
마지막으로 고려해 볼 수 있는 방식은 에어브러시 도색에서 활용하던 마스킹 작업입니다.
마스킹 테이프 등을 이용해 표면 일부를 가리고 도료를 도포하는 방식입니다. 뿌리고자 하는 부위의 표면만을 드러내어 작업해야 한다는 면에서는 실크 인쇄와 유사하나, 반복 작업이 쉽지 않습니다. 작업 과정에서 일일이 테이프를 부착하고 제거하는 과정이 필요하며, 위치를 잡기가 어렵고, 평평하지 못한 표면에서 틈새가 생길 위험성도 있기 때문에 자주 사용하고 있지는 않습니다.
이 외에도 컬러프린팅을 이용하여 추가 작업 없이 프린팅하거나, 음각 혹은 양각으로 프린팅하여 로고를 새기는 방법도 있습니다. 한양3D팩토리에서는 간혹 레이저 각인을 진행하기도 합니다. 디자인 목업을 목적으로 한다면, 로고의 표현방식과 그에 따른 효과도 비교하여 결정하기를 추천해 드립니다.
주의할 점
1. 제품 형상
간혹 제품의 생김새에 따라 작업이 어려운 부분도 있습니다.
①결합 제품의 연결부, ②도구가 들어가기 어려운 제품 내부나 틈새 등입니다.
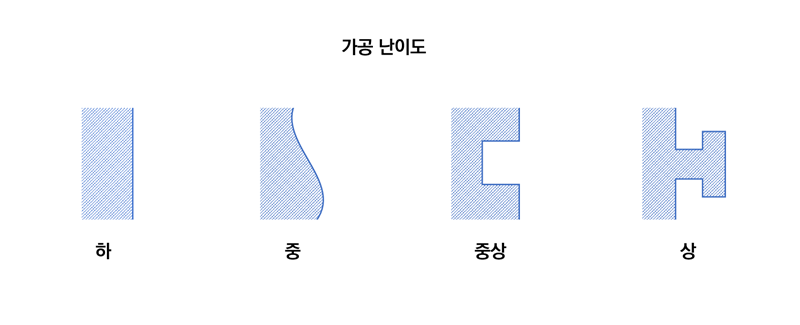
영역이 세밀하거나, 너무 들어가 있거나, 가려진 구조를 가지고 있다면 후가공이 어려울 수 있습니다. 작업이 불가능하거나, 추가 비용이 발생할 수 있기 때문에 형태가 복잡한 제품이라면 이 부분을 꼭 체크해 보시길 바랍니다. 더하여 대부분의 후가공 작업은 제품 외관 위주로 퀄리티를 높이는 작업이기에, 일반적으로는 내부 표면 정리 및 도색을 진행하지 않습니다. 비용을 추가로 지불하여 도색을 요청할 수는 있으나, 샌딩이 불가능한 내부라면 자연히 도색 퀄리티까지 떨어지게 됩니다. 색상이 있는 제품 내부를 원한다면 추가적인 후가공 대신 처음부터 표면 품질이 좋은 공법을 선택하여 진행하거나, 컬러 프린팅을 진행하여 대체할 수 있습니다.
2. 제품 두께
염색을 제외한 과정은 기존 제품 위에 가공면이 올라가는 방식으로 진행됩니다.
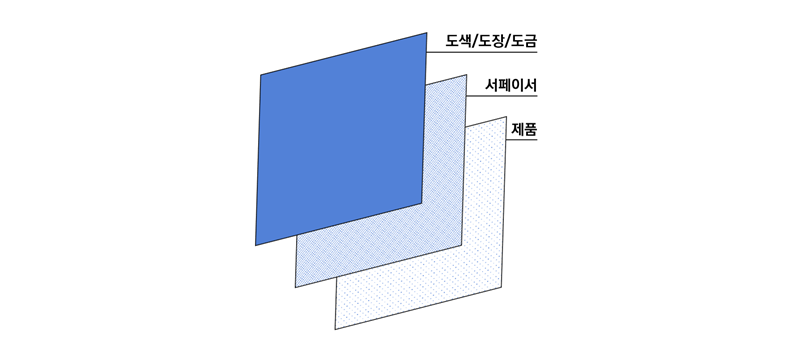
퍼티, 서페이서, 도색, 도장, 도금면이 올라가다 보면 완성품 두께에 미세한 차이가 생길 수 있습니다. 이는 진행하는 가공 단계와 후가공 표면 형태에 따라 다르며 밀리미터 기준 소수점 한 자릿수 이하의 미세한 차이로, 제품의 형상을 변형시킬 정도는 아닙니다. 그러나 결합이 필요한 제품이라면 공차 차이가 생길 수 있다는 점을 설계 과정에서부터 염두에 두어야 합니다.
이 밖에도 소재나 공법에 따라, 후가공 추천 여부가 달라집니다.
예를 들어 Agilus, Rubber-like, Silicon 등 고무 질감이 나는 소재에 에어브러시 도색을 진행하면 색이 잘 벗겨집니다. 도색을 할 수는 있으나 말랑하고 잘 휘어지는 소재일수록 도색면이 떨어지기 쉽기 때문에 추천 드리지 않으며, 같은 소재로 컬러프린팅을 진행하는 것이 나을 수 있습니다. 이렇게 퀄리티 높은 제품을 구현하려면 제품 구상 외에도 실현 가능한 부분인지에 따라 세세한 디테일을 신경 써야 하기에 믿을 만한 전문가와의 상담이 필요합니다.
마치며
지금까지 모든 출력물에 적용할 수 있는 후가공 과정에 대해 말씀드렸습니다.
후가공 결과물은 출력물의 소재, 출력 방식, 생김새에 따라 차이가 있습니다.
제품에 어울리는 후가공 과정을 선별하여 진행하시면 만족스러운 결과물을 얻으실 수 있습니다.
한양3D팩토리는 고객사의 목적과 상황을 고려하여 최적의 공정을 추천드리고, 맞춤 제작을 진행하고 있습니다.
제품에 알맞 후가공을 추천 받고 싶으시거나 제작 비용과 기간 등 자세한 사항이 궁금하시다면,
홈페이지 우측 상단이나 아래 배너의 제작 문의를 눌러 자세한 내용을 무료로 상담하실 수 있습니다.
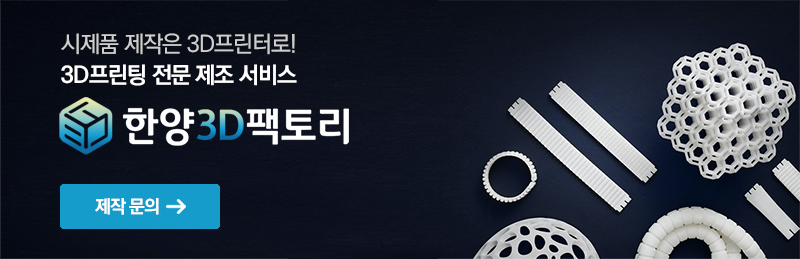